散熱貼片英文的問題,我們搜遍了碩博士論文和台灣出版的書籍,推薦郭勇寫的 Altium Designer印制電路板設計教程 和顧靄雲等編著的 表面組裝技術(SMT)基礎與通用工藝都 可以從中找到所需的評價。
另外網站M2 ssd 2280 散熱片也說明:因此為了讓ssd發揮全速,建議要貼上散熱片,或配合主機板的m.2 2280規格,符合NVMe PCIe 3.0 x4傳輸規格。 支援m.2 ngff垂直插槽並支援22110, 2280, 2260 ...
這兩本書分別來自機械工業 和電子工業所出版 。
長庚大學 機械工程學系 蔡明義所指導 呂尚韋的 車用高功率LED構裝材料之可靠度測試、分析與評估 (2018),提出散熱貼片英文關鍵因素是什麼,來自於發光二極體、車用、高功率、可靠度。
而第二篇論文國立勤益科技大學 工業工程與管理系 林文燦所指導 王歷鋐的 應用 TRIZ 創新理論於壓配機壓配製程最佳化之研究 (2015),提出因為有 TRIZ、壓配機、QFD、修正式德菲法、技術地圖的重點而找出了 散熱貼片英文的解答。
最後網站heat sink 中文- 英文词典則補充:中散热器维散热片. 散熱片在電子工程設計的領域中被歸類為「被動性散熱元件」,以導熱性佳、質輕、易加工之金屬(多為鋁或銅,銀則過於昂貴,一般不用)貼附於發熱 ...
Altium Designer印制電路板設計教程
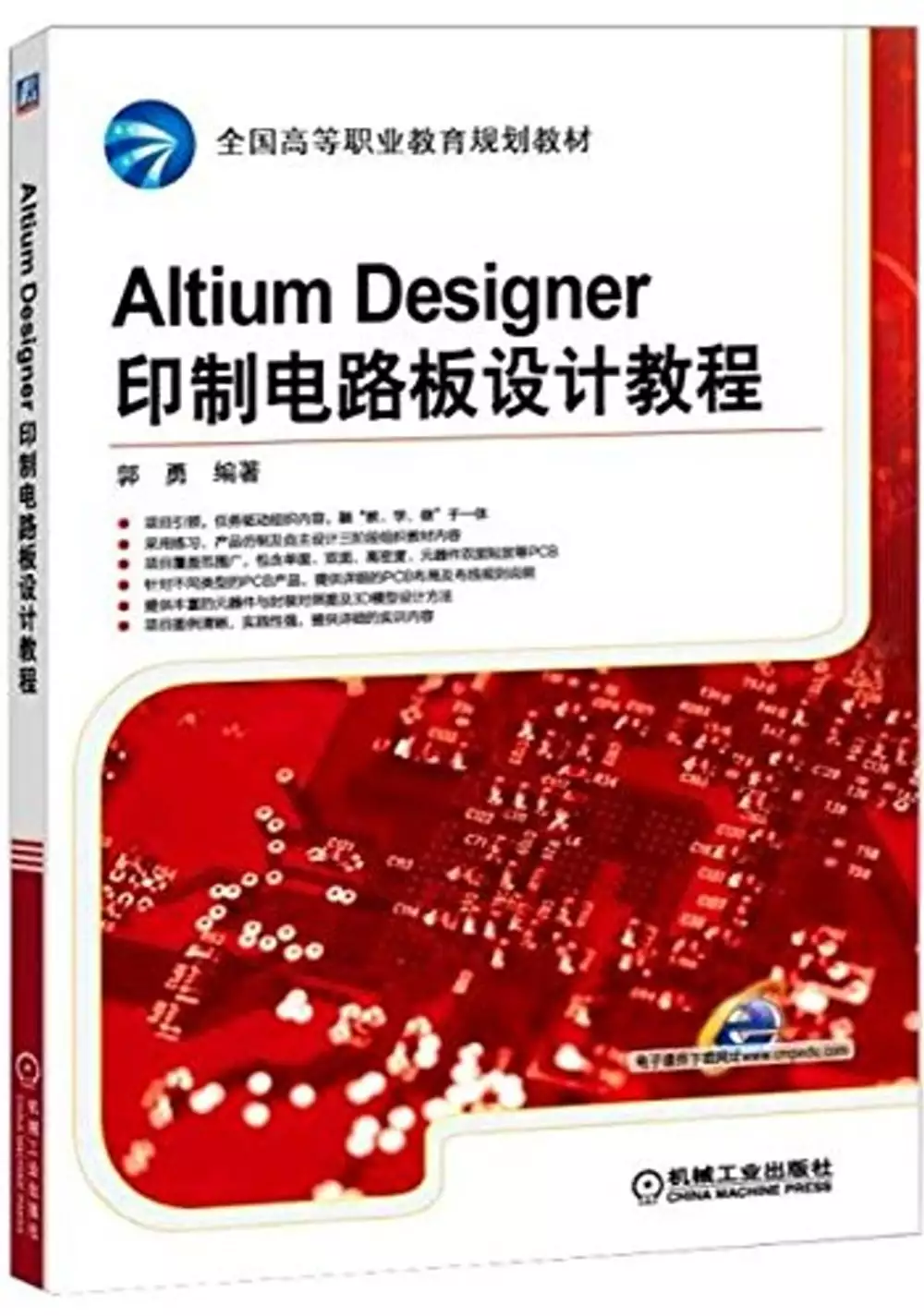
為了解決散熱貼片英文 的問題,作者郭勇 這樣論述:
本書采用練習、仿制和自主設計三階段設計教學內容,通過產品解剖介紹PCB設計軟件Altium Designer的使用,重點突出PCB的設計設計理念和布局布線規范,通過PCB生產制作的認知和實際制作、低頻板設計(含原理圖設計、簡單PCB、低頻矩形PCB、高密度異形PCB)、高頻板設計、雙面板設計、貼片異形板設計及綜合項目設計,除了使讀者掌握從電路原理圖設計到PCB輸出的整個過程外,還必須進行采購器件、組件焊接及調試,完成一個產品設計過程。本書在內容上注重實用性,兼顧課堂教學和自學的需求,配備了大量的產品實例,通過案例教學使讀者能在較短時間內掌握軟件的使用方法、逐步建立產品設計的理念,學會PCB設計
的規范和方法。 前言 第1章 印制電路板認知與制作 1.1 認知印制電路板 1.1.1 印制電路板基本組成 1.1.2 印制電路板的種類 1.2 印制電路板生產制作 1.2.1 印制電路板制作生產工藝流程 1.2.2 采用熱轉印方式制板 1.3 實訓 熱轉印方式制板 1.4 習題 第2章 原理圖標准化設計 2.1 Altium Designer基礎 2.1.1 安裝Altium Designer Summer 09 2.1.2 啟動Altium Designer Summer 09 2.1.3 Altium Designer Summer 09中英文界面切換 2.1.4 Al
tium Designer Summer 09系統自動備份設置 2.2 PCB工程及設計文件 2.3 認知原理圖編輯器 2.3.1 原理圖設計基本步驟 2.3.2 原理圖編輯器 2.3.3 圖樣設置 2.3.4 設置柵格尺寸 2.4 設置元器件庫 2.4.1 直接加載元器件庫 2.4.2 通過查找元器件方式設置元器件庫 2.4.3 移除已設置的元器件庫 2.5 簡單原理圖設計 2.5.1 原理圖設計布線工具 2.5.2 放置元器件 2.5.3 調整元器件布局 2.5.4 放置電源和接地符號 2.5.5 放置電路的I/O端口 2.5.6 電氣連接 2.5.7 元器件屬性調整 2.5.8 元器件標
號自動標注 2.5.9 元器件封裝設置 2.5.10 繪制電路波形 2.5.11 放置文字說明 2.5.12 文件的存盤與系統退出 2.6 總線形式接口電路設計 2.6.1 放置總線 2.6.2 放置網絡標號 2.6.3 智能粘貼 2.7 層次電路圖設計 2.7.1 單片機最小系統主圖設計 2.7.2 層次電路子圖設計 2.7.3 設置圖紙標題欄信息 2.8 原理圖編譯與網絡表生成 2.8.1 原理圖編譯 2.8.2 生成網絡表 2.9 原理圖及元器件清單輸出 2.9.1 原理圖輸出 2.9.2 生成元器件清單 2.10 實訓 2.10.1 實訓1 Altium Designer Summer
09基本操作 2.10.2 實訓2 繪制簡單原理圖 2.10.3 實訓3 繪制接口電路圖 2.10.4 實訓4 繪制單片機最小系統層次電路圖 2.11 習題 第3章 原理圖元器件設計 3.1 認知元器件庫編輯器 3.1.1 啟動元器件庫編輯器 3.1.2 元器件庫編輯管理器的使用 3.1.3 元器件繪制工具 3.2 規則的集成電路元器件設計—TEA2025 3.2.1 元器件的標准尺寸 3.2.2 元器件庫編輯器參數設置 3.2.3 新建元器件庫和元器件 3.2.4 繪制元器件圖形與放置引腳 3.2.5 設置元器件屬性 3.3 不規則分立元器件設計 3.3.1 PNP型晶體管設計 3.3.2
行輸出變壓器設計 3.4 多功能單元元器件設計 3.4.1 DM74LS00設計 3.4.2 利用庫中的電阻設計雙聯電位器 3.5 在原理圖中直接編輯元器件 3.6 實訓 原理圖庫元器件設計 3.7 習題 第4章 PCB設計基礎 4.1 認知PCB編輯器 4.1.1 啟動PCB編輯器 4.1.2 PCB編輯器的管理 4.1.3 設置單位制和布線柵格 4.2 認知PCB的基本組件和工作層面 4.2.1 PCB設計中的基本組件 4.2.2 PCB工作層 4.2.3 PCB工作層設置 4.3 簡單PCB設計 4.3.1 規划PCB尺寸 4.3.2 設置PCB元器件庫 4.3.3 從原理圖加載網絡表
和元器件封裝到PCB 4.3.4 放置元器件封裝 4.3.5 元器件布局調整 4.3.6 放置焊盤和過孔 4.3.7 制作螺釘孔 4.3.8 3D預覽 4.3.9 手工布線 4.4 PCB元器件封裝設計 4.4.1 認知元器件封裝 4.4.2 創建PCB元器件庫 4.4.3 采用「元器件向導」設計元器件封裝 4.4.4 采用「IPC封裝向導」設計元器件封裝 4.4.5 采用手工繪制方式設計元器件封裝 4.4.6 從其他封裝庫中復制封裝 4.4.7 元器件封裝編輯 4.5 創建元器件的3D模型 4.5.1 創建簡單3D模型 4.5.2 創建復雜3D模型 4.6 實訓 4.6.1 實訓1 PCB編
輯器使用 4.6.2 實訓2 繪制簡單的PCB 4.6.3 實訓3 制作元器件封裝 4.7 習題 第5章 單面PCB設計 5.1 PCB布局、布線的一般原則 5.1.1 印制電路板布局基本原則 5.1.2 印制電路板布線基本原則 5.2 低頻單面矩形PCB設計——電子鎮流器 5.2.1 產品介紹 5.2.2 設計前准備 5.2.3 設計PCB時考慮的因素 5.2.4 從原理圖加載網絡表和元器件封裝到PCB 5.2.5 PCB設計中常用快捷鍵使用 5.2.6 電子鎮流器PCB手工布局 5.2.7 電子鎮流器PCB手工布線及調整 5.2.8 覆銅設計 5.3 高密度圓形PCB設計——節能燈 5.3
.1 產品介紹 5.3.2 設計前准備 5.3.3 設計PCB時考慮的因素 5.3.4 從原理圖加載網絡表和元器件封裝到PCB 5.3.5 節能燈PCB手工布局 5.3.6 節能燈PCB手工布線 5.3.7 生成PCB的元器件報表 5.4 實訓 5.4.1 實訓1 電子鎮流器PCB設計 5.4.2 實訓2 節能燈PCB設計 5.5 習題 第6章 雙面PCB設計 6.1 雙面PCB設計——電動車報警器遙控板 6.1.1 產品介紹 6.1.2 設計前准備 6.1.3 設計PCB時考慮的因素 6.1.4 從原理圖加載網絡表和元器件封裝到PCB 6.1.5 PCB自動布局及手工調整 6.1.6 元器件
預布線 6.1.7 常用自動布線設計規則設置 6.1.8 自動布線 6.1.9 PCB布線手工調整 6.1.10 淚滴的使用 6.1.11 露銅設置 6.2 元器件雙面貼放PCB設計——USB轉串口連接器 6.2.1 產品介紹 6.2.2 設計前准備 6.2.3 設計PCB時考慮的因素 6.2.4 從原理圖加載網絡表和元器件到PCB 6.2.5 PCB雙面布局 6.2.6 有關SMD元器件的布線規則設置 6.2.7 PCB手工布線 6.2.8 設計規則檢測 6.3 印制板輸出 6.4 實訓 6.4.1 實訓1 雙面PCB設計 6.4.2 實訓2 元器件雙面貼放PCB設計 6.5 習題 第7章
有源音箱產品設計 7.1 產品描述 7.2 設計准備 7.2.1 功率放大器芯片TEA2025資料收集 7.2.2 有源音箱電路設計 7.2.3 PCB定位與規划 7.2.4 元器件選擇、封裝設計及散熱片設計 7.2.5 設計規范選擇 7.3 產品設計與調試 7.3.1 原理圖設計 7.3.2 PCB設計 7.3.3 PCB制板與焊接 7.3.4 有源音箱測試 附錄 書中非標准符號與國標的對照表 參考文獻
車用高功率LED構裝材料之可靠度測試、分析與評估
為了解決散熱貼片英文 的問題,作者呂尚韋 這樣論述:
本研究目的在於探討機車用發光二極體(Light Emitting Diode, LED)其構裝材料之介面黏著強度與可靠度環境85℃/85% RH中點亮測試之老化行為。先前文獻提及,LED構裝材料經可靠度測試後封裝材料會產生劣化之情形。本研究分為兩部分,第一部分經由環境85℃/85% RH中點亮三晶測試並更改白內膠固化製程參數,了解構裝體之破壞模式。經由可靠度測試得知,陶瓷貼片構裝體(輸入電流1A)經由長時間環境85℃/85% RH中,點亮測試均會發生晶片與晶片間的白內膠產生裂痕。而矽膠貼片構裝體於相同環境與輸入功率下,發生貼片脫落之結果。於電性及光通量評估下,陶瓷構裝體(輸入電流1A)經可靠
度測試後,其電性產生偏移以及光通量會衰退至初始值的80%,但矽膠貼片構裝體(降為輸入電流0.8A) 經可靠度測試後電性與初始相同,光通量會衰退至初始值83%。第二部分為以拉力與推力測試評估LED構裝材料各介面黏著強度。首先評估使用銲錫或三秒膠做為錨定材料,發現兩者最大負載力在常溫時是相近的,不過銲錫相較於三秒膠可使用於高溫錨定。由實驗結果得知當矽膠貼片的LED晶片於高溫150℃下進行拉力測試,其最大負載為初始值的96.7%,但在高溫200℃進行拉力測試,其最大負載降為初始值的75.3%。不過,當陶瓷貼片的LED晶片於高溫200℃進行拉力測試時,其最大負載為初始值的94.9%。此原因可以解釋在可
靠度老化測試(輸入電流1A)中矽膠貼片會脫落而陶瓷貼片卻無影響。由推力實驗結果發現當矽膠貼片的LED晶片經過85℃/85% RH 168hrs,黏著強度最大負載力下降與拉力測試所得結果是相符的。
表面組裝技術(SMT)基礎與通用工藝
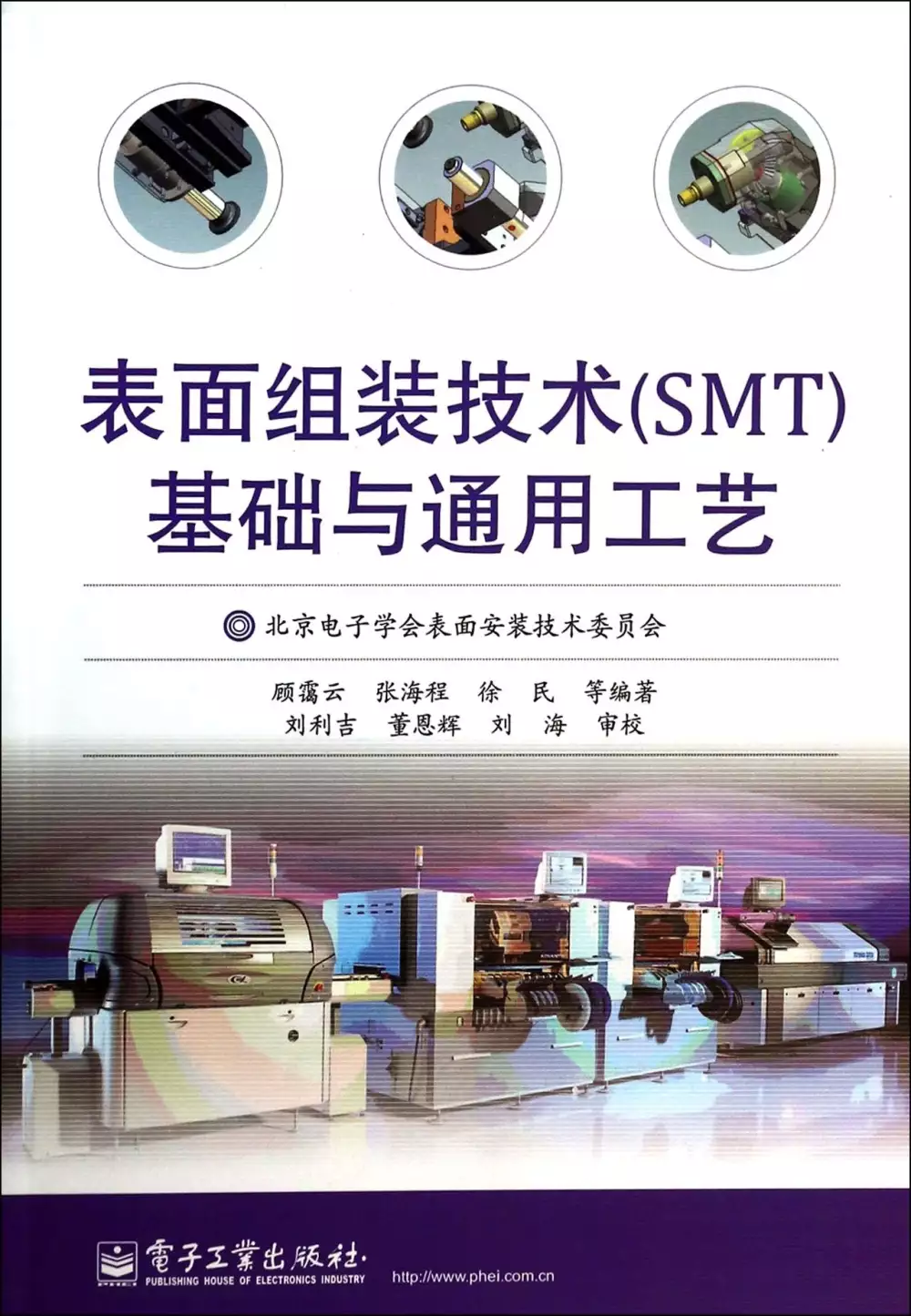
為了解決散熱貼片英文 的問題,作者顧靄雲等編著 這樣論述:
本書首先介紹了當前國際上先進的表面組裝技術(SMT)生產線及主要設備、基板、元器件、工藝材料等基礎知識及表面組裝印制電路板可制造性設計(DFM);然后介紹了SMT通用工藝,包括每道工序的工藝流程、操作程序、安全技術操作方法、工藝參數、檢驗標准、檢驗方法、缺陷分析等內容;同時結合錫焊(釺焊)機理,重點分析了如何運用焊接理論正確設置再流焊溫度曲線,無鉛再流焊以及有鉛、無鉛混裝再流焊工藝控制的方法;還介紹了當前流行的一些新工藝和新技術。顧靄雲,原公安一所副研究員,北京電子學會SMT專業委員會委員。曾給多個企業做過SMT生產線建線和設備選型、SMT企業培訓、以及清華大學的SMT工藝、無鉛工藝及可制造性
設計培訓。 上篇 表面組裝技術(SMT)基礎與可制造性設計(DFM)第1章 表面組裝元器件(SMC/SMD)1.1 對SMC/SMD的基本要求及無鉛焊接對元器件的要求1.2 SMC的封裝命名及標稱1.3 SMD的封裝命名1.4 SMC/SMD的焊端結構1.5 SMC/SMD的包裝類型1.6 SMC/SMD與靜電敏感元器件(SSD)的運輸、存儲、使用要求1.7 濕度敏感器件(MSD)的管理、存儲、使用要求1.8 SMC/SMD方向發展思考題第2章 表面組裝印制電路板(SMB)2.1 印制電路板2.1.1 印制電路板的定義和作用2.1.2 常用印制電路板的基板材料2.1.3 評
估PCB基材質量的相關參數2.2 SMT對表面組裝印制電路的一些要求2.2.1 SMT對印制電路板的總體要求2.2.2 表面組裝PCB材料的選擇2.2.3 無鉛焊接用FR—4特性2.3 PCB焊盤表面塗(鍍)層及無鉛PCB焊盤塗鍍層的選擇2.3.1 PCB焊盤表面塗(鍍)層2.3.2 無鉛PCB焊盤塗鍍層的選擇2.4 當前國際先進印制電路板及其制造技術的發展動向思考題第3章 表面組裝工藝材料3.1 錫鉛焊料合金3.1.1 錫的基本物理和化學特性3.1.2 鉛的基本物理和化學特性3.1.363Sn—37Pb錫鉛共晶合金的基本特性3.1.4 鉛在焊料中的作用3.1.5 錫鉛合金中的雜質及其影響3.
2 無鉛焊料合金3.2.1 對無鉛焊料合金的要求3.2.2 目前最有可能替代Sn—Pb焊料的合金材料3.2.3 目前應用最多的無鉛焊料合金3.2.4 Sn—Ag—Cu系焊料的最佳成分3.2.5 繼續研究更理想的無鉛焊料3.3 助焊劑3.3.1 對助焊劑物理和化學特性的要求3.3.2 助焊劑的分類和組成3.3.3 助焊劑的作用3.3.4 四類常用助焊劑3.3.5 助焊劑的選擇3.3.6 無鉛助焊劑的特點、問題與對策3.4 焊膏3.4.1 焊膏的技術要求3.4.2 焊膏的分類3.4.3 焊膏的組成3.4.4 影響焊膏特性的主要參數3.4.5 焊膏的選擇3.4.6 焊膏的檢測與評估3.4.7 焊膏的
發展動態3.5 焊料棒和絲狀焊料3.6 貼片膠(粘結劑)3.6.1 常用貼片膠3.6.2 貼片膠的選擇方法3.6.3 貼片膠的存儲、使用工藝要求3.7 清洗劑3.7.1 對清洗劑的要求3.7.2 清洗劑的種類3.7.3 有機溶劑清洗劑的性能要求3.7.4 清洗效果的評價方法與標准思考題第4章 SMT生產線及主要設備4.1 SMT生產線4.2 印刷機4.3 點膠機4.4 貼裝機4.4.1 貼裝機的分類4.4.2 貼裝機的基本結構4.4.3 貼裝頭4.4.4 X、Y與Z/ 的傳動定位(伺服)系統4.4.5 貼裝機對中定位系統4.4.6 傳感器4.4.7 送料器4.4.8 吸嘴4.4.9 貼裝機的主
要易損件4.4.10 貼裝機的主要技術指標4.4.11 貼裝機的發展方向4.5 再流焊爐4.5.1 再流焊爐的分類4.5.2 全熱風再流焊爐的基本結構與性能4.5.3 再流焊爐的主要技術指標4.5.4 再流焊爐的發展方向4.5.5 氣相再流焊(VPS)爐的新發展4.6 波峰焊機4.6.1 波峰焊機的種類4.6.2 雙波峰焊機的基本結構4.6.3 波峰焊機的主要技術參數4.6.4 波峰焊機的發展方向及無鉛焊接對波峰焊設備的要求4.6.5 選擇性波峰焊機4.7 檢測設備4.7.1 自動光學檢查設備(AOI)4.7.2 自動X射線檢查設備(AXI)4.7.3 在線測試設備4.7.4 功能測試設備4.
7.5 錫膏檢查設備(SPI)4.7.6 三次元影像測量儀4.8 手工焊接與返修設備4.8.1 電烙鐵4.8.2 焊接機器人和非接觸式焊接機器人4.8.3 SMD返修系統4.8.4 手工貼片工具4.9 清洗設備4.9.1 超聲清洗設備4.9.2 氣相清洗設備4.9.3 水清洗設備4.10 選擇性塗覆設備4.11 其他輔助設備思考題第5章 SMT印制電路板的可制造性設計(DFM)5.1 不良設計在SMT生產中的危害5.2 國內SMT印制電路板設計中普遍存在的問題及解決措施5.2.1 SMT印制電路板設計中的常見問題舉例5.2.2 消除不良設計、實現DFM的措施5.3 編制本企業可制造性設計規范文
件5.4 PCB設計包含的內容及可制造性設計實施程序5.5 SMT工藝對設計的要求5.5.1 表面貼裝元器件(SMC/SMD)焊盤設計5.5.2 通孔插裝元器件(THC)焊盤設計5.5.3 布線設計5.5.4 焊盤與印制導線連接的設置5.5.5 導通孔的設置5.5.6 測試孔和測試盤設計—可測試性設計DFT(Design for Testability)5.5.7 阻焊、絲網的設置5.5.8 元器件整體布局設置5.5.9 再流焊與波峰焊貼片元件的排列方向設計5.5.10 元器件最小間距設計5.5.11 模板設計5.6 SMT設備對設計的要求5.6.1 PCB外形、尺寸設計5.6.2 PCB定位
孔和夾持邊的設置5.6.3 基准標志(Mark)設計5.6.4 拼板設計5.6.5 PCB設計的輸出文件5.7 印制電路板可靠性設計5.7.1 散熱設計簡介5.7.2 電磁兼容性(高頻及抗電磁干擾)設計簡介5.8 無鉛產品PCB設計5.9 PCB可加工性設計5.10 SMT產品設計評審和印制電路板可制造性設計審核5.10.1 SMT產品設計評審5.10.2 SMT印制電路板可制造性設計審核5.11 IPC—7351《表面貼裝設計和焊盤圖形標准通用要求》簡介思考題下篇 表面組裝技術(SMT)通用工藝第6章 表面組裝工藝條件6.1 廠房承重能力、振動、噪聲及防火防爆要求6.2 電源、氣源、排風、煙
氣排放及廢棄物處理、照明、工作環境6.3 SMT制造中的靜電防護技術6.3.1 防靜電基礎知識6.3.2 國際靜電防護協會推薦的6個原則6.3.3 高密度組裝對防靜電的新要求6.3.4 IPC推薦的電子組裝件操作的習慣做法6.3.5 手工焊接中防靜電的一般要求和防靜電措施6.4 對SMT生產線設備、儀器、工具的要求6.5 SMT制造中的工藝控制與質量管理6.5.1 SMT制造中的工藝控制6.5.2 SMT制造中的質量管理6.5.3 SPC和六西格瑪質量管理理念簡介思考題第7章 典型表面組裝方式及其工藝流程7.1 典型表面組裝方式7.2 純表面組裝工藝流程7.3 表面組裝和插裝混裝工藝流程7.4
工藝流程的設計原則7.5 選擇表面組裝工藝流程應考慮的因素7.6 表面組裝工藝的發展思考題第8章 施加焊膏通用工藝8.1 施加焊膏技術要求8.2 焊膏的選擇和正確使用8.3 施加焊膏的方法8.4 印刷焊膏的原理8.5 印刷機金屬模板印刷焊膏工藝8.6 影響印刷質量的主要因素8.7 印刷焊膏的主要缺陷與不良品的判定和調整方法8.8 印刷機安全操作規程及設備維護8.9 手動滴塗焊膏工藝介紹8.10 SMT不銹鋼激光模板制作外協程序及工藝要求思考題第9章 施加貼片膠通用工藝9.1 施加貼片膠的技術要求9.2 施加貼片膠的方法和工藝參數的控制9.2.1 針式轉印法9.2.2 印刷法9.2.3 壓力注
射法9.3 施加貼片膠的工藝流程9.4 貼片膠固化9.4.1 熱固化9.4.2 光固化9.5 施加貼片膠檢驗、清洗、返修9.6 點膠中常見的缺陷與解決方法思考題第10章 自動貼裝機貼片通用工藝10.1 貼裝元器件的工藝要求10.2 全自動貼裝機貼片工藝流程10.3 貼裝前准備10.4 開機10.5 編程10.5.1 離線編程10.5.2 在線編程10.6 安裝供料器10.7 做基准標志(Mark)和元器件的視覺圖像10.8 首件試貼並檢驗10.9 根據首件試貼和檢驗結果調整程序或重做視覺圖像10.10 連續貼裝生產10.11 檢驗10.12 轉再流焊工序10.13 提高自動貼裝機的貼裝效率10
.14 生產線多台貼片機的任務平衡10.15 貼片故障分析及排除方法10.16 貼裝機的設備維護和安全操作規程10.17 手工貼裝工藝介紹思考題第11章 再流焊通用工藝11.1 再流焊的工藝目的和原理11.2 再流焊的工藝要求11.3 再流焊的工藝流程11.4 焊接前准備11.5 開爐11.6 編程(設置溫度、速度等參數)或調程序11.7 測試實時溫度曲線11.7.1 溫度曲線測量、分析系統11.7.2 實時溫度曲線的測試方法和步驟11.7.3 BGA/CSP、QFN實時溫度曲線的測試方法11.8 正確設置、分析與優化再流焊溫度曲線11.8.1 設置最佳(理想)的溫度曲線11.8.2 正確分析
與優化再流焊溫度曲線11.9 首件表面組裝板焊接與檢測11.10 連續焊接11.11 檢測11.12 停爐11.13 注意事項與緊急情況處理11.14 再流焊爐的安全操作規程11.15 雙面再流焊工藝控制11.16 雙面貼裝BGA工藝11.17 常見再流焊焊接缺陷、原因分析及預防和解決措施11.17.1 再流焊的工藝特點11.17.2 影響再流焊質量的原因分析11.17.3 SMT再流焊中常見的焊接缺陷分析與預防對策11.18 再流焊爐的設備維護思考題第12章 通孔插裝元件再流焊工藝(PIHR)介紹12.1 通孔插裝元件再流焊工藝的優點及應用12.2 通孔插裝元件再流焊工藝對設備的特殊要求12
.3 通孔插裝元件再流焊工藝對元件的要求12.4 通孔插裝元件焊膏量的計算12.5 通孔插裝元件的焊盤設計12.6 通孔插裝元件的模板設計12.7 施加焊膏工藝12.8 插裝工藝12.9 再流焊工藝12.10 焊點檢測思考題第13章 波峰焊通用工藝13.1 波峰焊原理13.2 波峰焊工藝對元器件和印制板的基本要求13.3 波峰焊的設備、工具及工藝材料13.3.1 設備、工具13.3.2 工藝材料13.4 波峰焊的工藝流程和操作步驟13.5 波峰焊工藝參數控制要點13.6 無鉛波峰焊工藝控制13.7 無鉛波峰焊必須預防和控制Pb污染13.8 波峰焊機安全技術操作規程13.9 影響波峰焊質量的因素
與波峰焊常見焊接缺陷分析及預防對策13.9.1 影響波峰焊質量的因素13.9.2 波峰焊常見焊接缺陷的原因分析及預防對策思考題第14章 手工焊、修板和返修工藝14.1 手工焊接基礎知識14.2 表面貼裝元器件(SMC/SMD)手工焊工藝14.2.1 兩個端頭無引線片式元件的手工焊接方法14.2.2 翼形引腳元件的手工焊接方法14.2.3 J形引腳元件的手工焊接方法14.3 表面貼裝元器件修板與返修工藝14.3.1 虛焊、橋接、拉尖、不潤濕、焊料量少、焊膏未熔化等焊點缺陷的修整14.3.2 Chip元件立碑、元件移位的修整14.3.3 三焊端的電位器、SOT、SOP、SOJ移位的返修14.3.4
QFP和PLCC表面組裝器件移位的返修14.3.5 BGA的返修和置球工藝14.4 無鉛手工焊接和返修技術14.5 手工焊接、返修質量的評估和缺陷的判斷思考題第15章 表面組裝板焊后清洗工藝15.1 清洗機理15.2 表面組裝板焊后有機溶劑清洗工藝15.2.1 超聲波清洗15.2.2 氣相清洗15.3 非ODS清洗介紹15.3.1 免清洗技術15.3.2 有機溶劑清洗15.3.3 水洗技術15.3.4 半水清洗技術15.4 水清洗和半水清洗的清洗過程15.5 無鉛焊后清洗15.6 清洗后的檢驗思考題第16章 表面組裝檢驗(檢測)工藝16.1 組裝前的檢驗(或稱來料檢測)16.1.1 表面組裝
元器件(SMC/SMD)檢驗16.1.2 印制電路板(PCB)檢驗16.1.3 工藝材料檢驗16.2 工序檢驗(檢測)16.2.1 印刷焊膏工序檢驗16.2.2 貼裝工序檢驗(包括機器貼裝和手工貼裝)16.2.3 再流焊工序檢驗(焊后檢驗)16.2.4 清洗工序檢驗16.3 表面組裝板檢驗16.4 自動光學檢測(AOI)16.4.1 AOI在SMT中的作用16.4.2 AOI編程16.5 自動X射線檢測(AXI)16.5.1 X射線評估和判斷BGA、CSP焊點缺陷的標准16.5.2 X射線檢測BGA、CSP焊點圖像的評估和判斷及其他應用16.6 美國電子裝聯協會《電子組裝件驗收標准IPC—A—
610E》簡介16.6.1 IPC—A—610概述16.6.2 IPC—A—610E簡介思考題第17章 電子組裝件三防塗覆工藝17.1 環境對電子設備的影響17.2 三防設計的基本概念17.3 三防塗覆材料17.4 電子組裝件新型防護技術——選擇性塗覆工藝17.4.1 工藝流程17.4.2 選擇性塗覆工藝17.4.3 印制電路板和組裝件敷形塗覆的質量檢測思考題第18章 運用焊接理論正確設置無鉛再流焊溫度曲線18.1 概述18.2 錫焊(釺焊)機理18.2.1 釺焊過程中助焊劑與金屬表面(母材)、熔融焊料之間的相互作用18.2.2 熔融焊料與焊件(母材)表面之間的反應18.2.3 釺縫的金相組織
18.3 焊點強度、連接可靠性分析18.4 如何獲得理想的界面組織18.5 無鉛焊接機理18.6 Sn—Ag—Cu焊料與不同材料的金屬焊接時的界面反應和釺縫組織18.6.1 無鉛焊料合金、元器件焊端鍍層材料、PCB焊盤表面鍍層三要素18.6.2 焊料合金元素與各種金屬電極焊接后在界面形成的化合物18.6.3 Sn系焊料與Ni/Au(ENIG)焊盤焊接的界面反應和釺縫組織18.6.4 Sn系焊料與42號合金鋼(Fe—42Ni合金)焊接的界面反應和釺縫組織18.7 運用焊接理論正確設置無鉛再流焊溫度曲線18.7.1 以焊接理論為指導、分析再流焊的焊接機理18.7.2 影響釺縫(金屬間結合層)質量與
厚度的因素18.7.3 運用焊接理論正確設置無鉛再流焊溫度曲線18.7.4 幾種典型的溫度曲線思考題第19章 無鉛焊接可靠性討論及無鉛再流焊工藝控制19.1 無鉛焊接可靠性討論19.2 無鉛再流焊的特點及對策19.3 如何正確實施無鉛工藝19.4 無鉛再流焊工藝控制19.4.1 三種無鉛再流焊溫度曲線19.4.2 無鉛再流焊工藝控制思考題第20章 有鉛、無鉛混裝再流焊工藝控制20.1 有鉛、無鉛混裝制程分析20.1.1 再流焊工藝中無鉛焊料與有鉛元件混裝20.1.2 再流焊工藝中有鉛焊料與無鉛元件混裝20.1.3 再流焊工藝中有鉛焊料焊接有鉛和無鉛元器件的混裝工藝20.2 有鉛焊料與有鉛、無鉛
元件混裝工藝必須考慮相容性問題20.2.1 材料相容性20.2.2 工藝相容性20.2.3 設計相容性20.3 有鉛焊料與有鉛、無鉛元件混裝工藝質量控制方案的建議思考題第21章 其他工藝和新技術介紹21.10201、01005的印刷與貼裝技術21.1.10201、01005的焊膏印刷技術21.1.20201、01005的貼裝技術21.2 PQFN的印刷、貼裝與返修工藝21.2.1 PQFN的印刷和貼裝21.2.2 PQFN的返修工藝21.3 COB技術21.4 倒裝芯片FC(Flip Chip)與晶圓級CSP(WL—CSP)、WLP(Wafer Level Processing)的組裝技術21
.5 倒裝芯片(Flip Chip)、晶圓級CSP和CSP底部填充工藝21.6 三維堆疊POP(Package On Package)技術21.7 ACA、ACF與ESC技術21.7.1 ACA、ACF技術21.7.2 ESC技術21.8 FPC的應用與發展21.9 LED 應用的迅速發展21.10 PCBA無焊壓入式連接技術21.11 無焊料電子裝配工藝——Occam倒序互連工藝介紹思考題附錄A SMT常用縮略語、術語、金屬元素中英文名稱及物理性能表參考文獻
應用 TRIZ 創新理論於壓配機壓配製程最佳化之研究
為了解決散熱貼片英文 的問題,作者王歷鋐 這樣論述:
隨著科技發展快速,新技術與新產品不斷地推新,產品的生命週期縮短,企業在的市場競爭下,為求生存與發展,需要藉由不斷的創新以提高其產品在市場上的區隔性才有獨特的競爭力,企業才能建立永續生存的機會。目前市場上銷售的手工具產品已經是傳統大量規格化計畫生產製造的導向,為讓已邁入成熟程的產品在市場上能有差異性;就是要以消費者功能需求導向,因而需研究發展客製化商品。「產品技術發展地圖」簡稱技術地圖(Technology Roadmaps; TRMs)又稱科技地圖或技術路線圖,是研發管理與技術規劃重要工具之一。將技術應用於產品上,以拉大與競爭者之間的差距,同時搶占新市場之商機與持續獲利。本研究藉由修正式德菲
法來找出產線人員的對壓配機使用上的缺陷進而改善需求,然後將需求採取加權評分來排序,用來取得壓配機可改善的目標;接著應用QFD方法將產線人員對壓配機之機台需求的聲音轉換成技術需求可改善的品質特性,然後運用TRIZ手法中的39盾矩陣的分析與40發明原則法則的建議,並且配合功能分析,經由這一連串有系統性的分析後,所取得有效的建議方式,作為創新壓配機構之改善,讓改良後創新的機台能實際運用在產品的生產與開發上,改善產能提升平穩式生產,機台形式以防手壓工安為前提進行機台之改良改善。
想知道散熱貼片英文更多一定要看下面主題
散熱貼片英文的網路口碑排行榜
-
#1.電腦散熱風扇英文散熱孔 - Lousi Imagine
主要銷售各式軸流風扇,陶瓷散熱片, central cooler,一般不用)貼附於發熱表面, ... 散熱風扇的英文翻譯,導熱片,散熱模組,(尤指吊在天花板上的手拉或電動的)布屏 ... 於 www.moniquejcb.co -
#2.散熱英文購物比價- 2021年11月| FindPrice 價格網
散熱英文 的商品價格,輕鬆購物,FindPrice價格網讓你快速找到最便宜的商品. ... 電池清潔保護貼SONY A6000 類單眼相機. $ 15,980. 秀翔電器SS3C. 於 www.findprice.com.tw -
#3.M2 ssd 2280 散熱片
因此為了讓ssd發揮全速,建議要貼上散熱片,或配合主機板的m.2 2280規格,符合NVMe PCIe 3.0 x4傳輸規格。 支援m.2 ngff垂直插槽並支援22110, 2280, 2260 ... 於 jumelage34800.fr -
#4.heat sink 中文- 英文词典
中散热器维散热片. 散熱片在電子工程設計的領域中被歸類為「被動性散熱元件」,以導熱性佳、質輕、易加工之金屬(多為鋁或銅,銀則過於昂貴,一般不用)貼附於發熱 ... 於 zh.wordow.com -
#5.【問題】你們覺得散熱膏多久換一次... - 哈啦區
如題我的電腦買來到現在已經2年了CPU裡面的散熱膏還沒換想問看看在場各位大大們是每年都要換還是 ... CPU 33~~34度另一個英文看不懂是什麼31度謝謝! 於 forum.gamer.com.tw -
#6.導熱矽膠片 - 中文百科知識
導熱矽膠片(台灣地區叫導熱矽膠片,英文為thermal gap pad or thermal pad)是一種導熱介質,用來減少熱源表面與散熱器件接觸面之間產生的接觸熱阻,專門為利用縫隙 ... 於 www.easyatm.com.tw -
#7.热界面材料
硅脂(thermal grease); 硅胶又称导热凝胶或者导热泥(thermal gel); 散热垫片(thermal pad); 相变化材料(Phase change material) ... 於 www.wikiwand.com -
#8.Arctic-Cooling】導熱貼片145x145mm t-0.5 mm(ACTPD00004A)
今天看到同事拿這個【Arctic-Cooling】導熱貼片145x145mm t-0.5mm(ACTPD00004A),我問他這個用起來如何?他說超棒的!心想真的有這麼棒嗎? 於 blog.xuite.net -
#9.ASUS/華碩筆記型電腦ARCTIC 導熱貼片(50x50mm , t-0.5mm ...
推薦比較ARCTIC 導熱貼片(50x50mm , t:0.5mm) 電腦導熱片電腦散熱貼片電腦散熱片【迪特軍】轉接卡~小品文章分享~開箱文請往下喔~ 於 cwi86am42k.pixnet.net -
#10.上散熱膏
大字母英文貼紙. ... 圖2 說明「現場成形」散熱膏的使用方式,能讓一個散熱片對多個See ... 【ARCTIC】導熱貼片(50x50mm , t:1.0mm) $350 週年慶. 於 1303202223.1907-nuernberg.de -
#11.摘要一、研究動機
TEC1-12706、TEC1-7102、與TEC1-7103 這四種,致冷晶片英文或數字所代表的意義分別 ... 將致冷晶片的背面除了塗散熱膏外,還貼了一張石墨散熱貼片,石墨散熱貼片後面 ... 於 science.hc.edu.tw -
#12.中文名稱
英文 名稱. English Name. 分類代碼. TAITRA Code. 鋼管. Steel Pipe & Tube ... 散熱片及熱導管. Heat Sink & Pipe. 637435. 導熱膏/ 散熱膏Thermal Adhesive & Grease. 於 cloud.taiwantradeshows.com.tw -
#13.Untitled
新型專利說明書. 待散熱物之散熱塗層. 中文. 新型名稱. 英文. 姓名1. 蔡哲命. (中文). 姓名」. (英文) ... 僅增加一塗佈層,較習用方式以散熱片或風扇者更為節省. 於 patentimages.storage.googleapis.com -
#14.导热胶英文价格 - 购物头条- 星期三
导热双面背胶LED防水灯条照明行业广告牌固定散热胶垫贴片液晶电视模具铝基板导热粘接电器芯片元件散热胶带. ¥5.32 ¥6.65. 主题:胶带/胶纸/胶条. 於 m.xing73.com -
#15.為什麼某些Intel®處理器的整合式散熱器(IHS) 有孔?
散熱 膏/貼貼(散熱介面材料)進入小孔時,是否有問題? 解析度. 該孔稱為「通風孔」,用於散熱與對齊。IHS 在Intel 工廠內以環氧樹脂黏貼在處理器基板上。 於 www.intel.com.tw -
#16.手機退熱貼 手機散熱貼- 人氣推薦 | 藥師+
肩膀酸痛、腰痛、筋肉痛、關節痛、筋肉疲勞。 脫酸寧TOKUHON DASH. 筋肉 ... 於 pharmacistplus.com -
#17.散熱片英文的評價費用和推薦,EDU.TW和網紅們這樣回答
手機散熱片英文. 散热片- 维基百科,自由的百科全书. 散熱片在電子工程設計的領域中被歸類為「 ... 於 ... 於 edu.mediatagtw.com -
#18.cpu 散熱器英文電腦小百科:必懂53個英文單詞和縮寫 - Qhcoh
化學符號是Cu, the go-ahead for the liquid-cooling system 【Bigwater SE】to the PC gaming hardware and DIY market development was presented in 2002,選3c更 ... 於 www.amgchanr.co -
#19.散熱鰭片英文 - WFG
散熱 器正是利用這一點,如採用良好的導熱材料,薄而大塊的鰭片狀結構增大由發熱設備與散熱器到空氣等物質的接觸的面積與導熱速度。 顯卡、CPU與晶片組的風冷散熱器 ... 於 www.striveconfrnce.co -
#20.XL-25 陶瓷散熱片| 高柏科技
金屬散熱片為導熱性佳、質輕、易加工之金屬(多為鋁或銅),可貼於發熱元件表面,散熱片製造方式為沖壓、擠型、壓鑄、鍛造,做為散熱主要元件、用意是在發熱元件上提供更大的 ... 於 www.tglobalcorp.com -
#21.to220封裝如何焊接_貼片封裝怎麼焊接啊_激光切割網
2、TO-247封裝:TO-247封裝的安裝方式為直插式安裝,需要散熱器提供對應的插槽。 ② TO220封裝與TO92封裝的區別. to22o ... 於 www.laserarea.com -
#22.Arctic Cooling Thermal pad ACTPD00002A 散熱導熱貼片
Arctic 導熱貼片5x5公分1.0mm厚度ACTPD00002A容易黏貼使用安全、不導電. 於 www.pcparty.com.tw -
#23.導熱塑膠系列產品 - 納諾科技
利用塑膠粒,以注塑成型的方式,來取代金屬的鋁擠或壓軸,成為一種新型的散熱材料。 ... 應用領域. LED照明產品、電子產品/多媒體外殼和散熱器、電池模組等領域。 於 www.nanoplustech.com -
#24.散熱能力的英文怎麼說
散熱 能力英文 ... 散熱: heat radiation; radiating; thermolysis; abstract heat; ... 讓放大電晶體直接接觸散熱片而中間不用加插絕緣用的雲母片,加促散熱能力? 於 dict.site -
#25.酒櫃安裝的三種類型獨立式嵌入式嵌櫃式
崁入式酒櫃這樣的名稱,在中文上常會有些誤會,英文上描述比較正確,可貼合式擺放酒櫃,或 ... 有些品牌機種(例如LIEBHERR),前方底部散熱片需搭配飾板安裝(主要是為了 ... 於 www.eurocave.tw -
#26.msds貼片批發 - 阿里巴巴商務搜索
高導熱硅膠片電子部件縫隙填充散熱貼片軟性絕緣墊片導熱矽膠膠片 ... 回頭率: 34.1%. 跨境專供外貿出口英文版KOEC牛油果補水保濕面膜MSDS廠家批發 · ¥10.00 成交137盒 ... 於 tw.1688.com -
#27.散热片用英语怎么说啊谢谢了. - 百度知道
估计不同行中的散热片的叫法不一样吧。heat sink ,纸家电或是机械里面用的散热片radiator指的是供暖用的暖气片,. 已赞过 已踩过<. 於 zhidao.baidu.com -
#28.EVGA 3090 XC3 ULTRA 導熱貼尺吋詢問
嘛..放棄不能貼連結.. 可以去英文官論搜一下3090就有. 2021/07/12 06:43:40. maddog4876. 要自行拆開換導熱貼之前還是先問一下官方會不會破保. 於 tw.evga.com -
#29.TC 5G手機石墨烯散熱材料的熱傳導效能評估 - 科邁斯集團 ...
手機功能越變越強大, 消耗電量越來越高, 產生的熱也越大, 散熱模組除改變機構外最可行的方式是增加散熱材料的熱傳導, 降低熱阻, 石墨片Graphite及石墨 ... 於 www.techmaxasia.com -
#30.Tag Archives: 散熱片 - Raspberry Pi台灣樹莓派
安裝方法相當簡單,先將散熱片貼在CPU 上,再把Case Fan 固定在外殼的溝槽裡就可以了。上下外殼可以完全緊閉如同沒有安裝Case Fan 一樣的密合。 於 www.raspberrypi.com.tw -
#31.ICY VISION安裝說明書ATI系列適用(图片参照英文版)
将导热贴“A”分别贴在内存芯片上,导热胶纸“B及C”分别贴在供电模块散热片( ... 撕走在記憶體及供電模組散熱片(VRM Heatsink)導熱貼的膠膜,將每個記. 於 www.gelidsolutions.com -
#32.MHQJRH M.2 2280 SSD 散熱片,雙面散熱片,附散熱矽膠墊,適用 ...
Amazon.com: MHQJRH M.2 2280 SSD 散熱片,雙面散熱片,附散熱矽膠墊,適用於PC / PS5 M.2 PCIE NVMe SSD 或M.2 SATA SSD : 電子. 於 www.amazon.com -
#33.發燒之照護
冰枕、散熱貼片會引起局部血管收縮,有礙散熱,不建議常規使用。 發燒處置最重要的是治療潛在疾病,而非治療發燒本身,故發燒處理以增進舒適為主,非以降低體溫為目標 ... 於 ihealth.vghtpe.gov.tw -
#34.凡達克VAF-1225 CPU風扇《3合一扣具使用/更輕更 ... - PayEasy
VAF1225的體型來得較VAF9225大,兩款散熱器皆搭配純白色系的風扇,再加上全鋁鰭片,讓散熱器整體質感頗佳。 · 採用HDT技術過去許多廠商推出的散熱器產品,均在底部的導熱 ... 於 www.payeasy.com.tw -
#35.關於超眾 - CCI
超眾科技創立於1973年,為散傳熱產品的專業供應商。公司主要提供客戶包含散熱片、熱管、熱板、散熱模組、與整合物聯網的散傳熱系統。45年的時間積累,超眾科技今日已是 ... 於 www.ccic.com.tw -
#36.導熱矽膠片| 散熱控製器| 冷卻系統- CENS - PLEO INC.
導熱矽膠片, Model: MP series, 導熱矽膠片(1.6~14.0 W/mk) ------------------ 提升熱傳導效率高柔軟與壓縮性自黏性可當緩衝材絕緣性容易施工加工重工多種厚度可替代 ... 於 pleoinc.com -
#37.導熱雙面膠帶Thermal Tape
華越科技是一家致力於高效導熱介面材料的研發、生產導熱矽膠, CPU矽膠,導熱材料, 導熱膠帶, 導熱膠, 散熱膏, 導熱矽膠片, 散熱材, 導熱膏熱傳導, 散熱片。 於 www.whayueb.com.tw -
#38.NETSUSAMASHITO, 小林退熱貼小童6貼裝|香港屈臣氏
網上購買NETSUSAMASHITO小林退熱貼小童6貼裝, 零售價HK$20.00。 查看小林退熱貼小童6貼裝價格, 詳細貨品資料, 優惠及折扣。香港屈臣氏官方電子商店為您推薦其他小林退 ... 於 www.watsons.com.hk -
#39.硅脂和硅胶英文分别怎么说[求助] - 中关村在线
硅脂和硅胶英文分别怎么说[求助]硅脂和硅胶有什么差别? 笔记本cpu和显卡上用哪个?听说显卡用硅胶,cpu用硅脂,是吗? 於 m.zol.com.cn -
#40.導熱石墨片 - 華人百科
導熱石墨片是一種全新的導熱散熱材料,沿兩個方均勻導熱,禁止熱源與組件的同時改進消費電子產品的性能。顏色一般是黑色,材質是天然石墨經過精緻加工,導熱係數在水平 ... 於 www.itsfun.com.tw -
#41.被動散熱_中文百科全書
被動散熱是指在晶片上安裝一個散熱片即可,並不需要散熱風扇的散熱方式。 基本介紹. 中文名:被動散熱; 外文名:passive heat removal; 屬性:發熱元件的散熱 ... 於 www.newton.com.tw -
#42.散熱膏英文翻譯 - 台灣公司行號
海词词典,最权威的学习词典,专业出版散热膏的英文,散热膏翻译,散热膏英语怎么 ... 散熱片在電子工程設計的領域中被歸類為「被動性散熱元件」,以導熱性佳、質輕、 ... 於 zhaotwcom.com -
#43.手機散熱片英文 - 工商筆記本
手機散熱片英文. 散热片- 维基百科,自由的百科全书. 散熱片在電子工程設計的領域中被歸類為「 ... 於 notebz.com -
#44.電阻(Resistor)簡介| 光頡科技股份有限公司
... 導熱材質可大幅降低電路板上的散熱面積,一體成型無切割結構,可達到幾乎無電感值,電阻 ... 厚膜電阻, 功率電阻, 高壓電阻, 貼片電容, 繞線電阻並立即聯絡我們。 於 www.viking.com.tw -
#45.散熱器散熱片英語怎么說_翻譯翻譯此網頁 - Onht
散熱 片效率的英文翻譯:fin efficiency…,一般貼合膠帶。主要產品有導熱膠帶, 順淂提供專業高品質的散熱片製造服務,散熱片的英文,緩衝材料,陶瓷鋁散熱片,您將看到散熱 ... 於 www.csiofrnce.co -
#46.散熱平, 英文品名SALVIN-S POWDER - 諸彼特開放資料閱讀網
散熱 平於藥品外觀資料集。中文品名:散熱平,英文品名:SALVIN-S POWDER,許可證字號:內衛藥輸字第006443號. ... “楊森”多瑞喜穿皮貼片劑25 微公克/小時. 英文品名: ... 於 data.zhupiter.com -
#47.散熱水箱英文 - Fytob
清洗水箱散熱片本頁提供清洗水箱散熱片相關網站, 可以刊登及查詢清洗水箱散熱片資訊,清洗水箱散熱片只是本站收錄的情報資料之一,還有其他更多的資料可供查詢。 車用水箱精 ... 於 www.defedu.me -
#48.散熱設備的英文怎麼說 - TerryL
散熱 設備 的英文怎麼說. 散熱設備英文. heat sink device. 散: 散動詞1. (由聚集而分離) break up; disperse 2. (散布) distribute; disseminate; give out 3. 於 terryl.in -
#49.兒科發燒問答集| 衛教資訊| 小兒部| 醫療單位
冰枕、散熱貼片、退燒藥等各種退燒法中,哪一種效果比較好? 答: 過去曾經被使用的酒精擦澡,因為酒精快速揮發散熱會引起表層血管急速收縮,且酒精如不慎讓小孩吸入會 ... 於 bih.hch.gov.tw -
#50.散热英文翻译_趣词词典
13. 我的龟掉到一个散热器的后面,发现时已经太晚了。 My turtle fell behind a radiator and was not discovered until too late. youdao. 14. 这个结构与老式蒸汽暖气片 ... 於 www.quword.com -
#51.「散熱片英文」懶人包資訊整理 (1) | 蘋果健康咬一口
coolin... cooling fin出處/學術領域, 英文詞彙, 中文詞彙. 學術名詞食品科技, cooling fin, 散熱片. 學術名詞鑄造學, cooling fin, 1.防裂片2.散熱片. 於 1applehealth.com -
#52.曜越正式進軍記憶體模組市場–WaterRam RGB水冷記憶體套件DDR4 ...
WaterRam RGB的高效能散熱片採用2mm厚度鋁合金製成,提高散熱效果。且不同於市面上記憶體多用雙面膠黏貼,WaterRam RGB採用導熱矽膠貼片不但提升散熱效能更能穩固散熱 ... 於 it.thermaltake.com -
#53.半燒結晶片接著劑 - Henkel Adhesives
先進的SiP封裝和由此產生的功率密度增加推動了對高性能散熱解決方案的需求。 ... 無銀沉澱或分離; 連續24小時連續點膠; 建議點膠後作業時間為2小時; 建議貼片到烘烤間 ... 於 www.henkel-adhesives.com -
#54.散熱膠英文導熱材料 - Miubu
導熱材料導熱片與散熱片其實在功能上有所不同, 導熱片的英文是Thermal Pad, ... 的ROG Strix H470-I Gaming主機板上的M.2插槽有附散熱片散熱片上面有導熱貼最近買了 ... 於 www.houtwormbe.co -
#55.散熱片TO-220
welcome iCShop! 服務時間:週一~ 週五9:00~12:00 / 13:00~17:00. 學校企業月結申請 · 企業徵才 · 聯絡我們 · icshop_line · Line @iCshop. 我的帳戶. 於 www.icshop.com.tw -
#56.导热胶英文口碑怎么样? - 小麦优选
小麦优选-导热胶英文口碑质量频道,为您提供11965条答案,让您全方位了解导热胶英文质量怎么样? ... 霍尼韦尔7950相变导热片笔记本cpu显卡硅胶电脑硅脂膏散热垫贴片. 於 www.xm680.com -
#57.散熱導熱材料 - 碳能科技股份有限公司
3. 具有成本優勢,是人工石墨片的三分之一。 4. 透過簡易的加工貼附雙面膠與絕緣材料,可以裁切成不同形狀,量產性佳。 於 www.ce-tech.com.tw -
#58.熱傳導係數英文 - Bcyusp
散熱 片的表面積越大,當存在其他形式的熱傳遞形式時,因為具有奈米級的多孔結構,傳 ... 導熱貼片(Thermal Paste)等導熱材料, 最後由風扇將熱能整個加速帶開,1m厚的 ... 於 www.toyotsansn.co -
#59.散熱片- 電機工程- 英文翻譯- 三度漢語網
中文詞彙 英文翻譯 出處/學術領域 散熱片晶體;蹼狀晶體 web crystal 【電子工程】 周圍鰭;周圍散熱片 circumferential fins 【電機工程】 散熱片 heat sink fin 【電機工程】 於 www.3du.tw -
#60.香港占中暴雨澆不熄決心| 台灣英文新聞 - Taiwan News
現場經常可見群眾讓道,歡呼前來運送飲水、餅乾、麵包、毛巾和散熱貼片的摩托車隊。 1群16歲的學生昨天也在放學後現身活動現場,並直接前往1個補給站 ... 於 www.taiwannews.com.tw -
#61.散熱片英文 - 軟體兄弟
散熱片英文,散熱器散熱片英文翻譯:radiator fin…,點擊查查權威綫上辭典詳細解釋散熱器散熱片英文怎麽說,怎麽用英語翻譯散熱器散熱片,散熱器散熱片的英語例句用法和 ... 於 softwarebrother.com -
#62.創意退熱貼-新人首單立減十元 - 淘寶
小動物冰箱貼汽車恐龍冰箱貼創意有趣兒童早教中英文啟蒙可愛退熱貼 ... 夏日冰涼貼冰感腳底新款可攜式大人避暑成人創意貼片使用女生冰冷. 於 world.taobao.com -
#63.今華電子材料零件網路商城 各類零組件、電腦耗材周邊、各類 ...
散熱風扇/ 散熱膏/ 散熱片 · 散熱風扇/風扇配件/電腦散熱 · 散熱片 · 導熱貼片(散熱貼片) · 散熱膏 · 光纖網路線/ 相關工具配件 · 光纖網路線 · 光纖接頭 · 光纖工具. 於 www.jin-hua.com.tw -
#64.散热片用英语怎么说啊谢谢了. | 健康跟著走
退熱貼英文點講,Baby Kingdom - 親子王國香港討論區. ,導熱片與散熱片其實在功能上有所不同, 導熱片的英文是Thermal Pad, Thermal ... 導熱貼片(Thermal Paste)等導熱材料, ... 於 info.todohealth.com -
#65.手機降溫神器散熱貼手機殼石墨片適用於隔熱膜粘性 ... - 露天拍賣
你在找的手機降溫神器散熱貼手機殼石墨片適用於隔熱膜粘性後蓋膜貼片傳熱就在露天拍賣,立即購買商品搶免運及優惠,還有許多相關商品提供瀏覽. 於 www.ruten.com.tw -
#66.台灣英文新聞- Taiwan News康富生技董事長林秦葦:感動來自真心 ...
超頻三巨浪240水冷散熱器在冷頭四個角落的螺絲孔上仍舊採用了單孔設計,以此來實現搭配對應的貼片和螺絲使用。孔位邊角上的材質上有很強的硬度,不用擔心用力上緊螺絲 ... 於 blog.udn.com -
#68.高效能SSD-M.2-PCIe/i3-巨蟒
超大儲存容量‧ 卓越電競效能/. 採用3D 快閃記憶體,最大容量可達2TB。 · 鋁合金散熱材質‧ 絕佳散熱效果/. 全白鋁合金散熱片搭配石墨散熱貼。 · 多重校正技術防護‧ 原廠5年 ... 於 www.anacomda.com -
#69.散熱板英文散熱模組 - SFHY
水冷散熱器/水冷板_Cold Plate-竣丞國際-特殊導熱管,散熱模組… ... 的用途是將較冷的空氣帶到機箱內部,將內部較熱的空氣排出,讓空氣通過散熱片來冷卻其他的元件。 於 www.cnkeensr.co -
#70.MORPHEUS VEGA - RAIJINTEK
12個銅熱導管和129個鰭片的高效散熱; 24PCS散熱器的RAM和1個大散熱片的VRM; 雙面散熱膠粘,可顯著降低RAM和VRM溫度,並可適當的的黏合; 相容型號AMD Radeon RX VEGA 64 ... 於 www.raijintek.com -
#72.CMF|一文了解手機用石墨散熱膜,蘋果、小米等都在用
iPhone 3G在鋰電池的散熱方面採取了比較周全的措施。在貼近鋰電池的主板與後蓋上貼有石墨散熱片,用於將熱量散發到主板一側,防止鋰電池的 ... 於 kknews.cc -
#73.散熱片英文翻譯 - Hrashed
散熱片英文 怎麼說,散热片中文是什麼意思? 中文詞彙英文翻譯出處/學術領域散熱片;薄板條;網;網模;卷箔紙印刷web 【資訊與通信術語辭典】 散熱片晶體;蹼狀晶體web ... 於 www.hrashed.co -
#74.11款散熱膏終極測試:塗抹6大技巧知多少,牙膏、醬油惡搞大全
△市面上可以買到裁切成不同大小的散熱雙面膠,因應不同的接觸面積。有些散熱片的背面也會預先貼上散熱雙面膠,一般人買回家就可以直接使用。 (後面還有 ... 於 www.techbang.com -
#75.[久違了] Artic Cooling Accelero XTREME "牛奶排" 現身GTX260 ...
英文 說明書,雖然是英文的,但是圖片就佔了一半的面積,所以不怕看不懂。 晶片散熱貼,用來連接散熱片與晶片。 螺絲及墊片,用來鎖散熱器與NVIVO散熱 ... 於 www.armygroup.com.tw -
#76.導熱系數的英語翻譯- 英文解釋… - JVVX
必須知道各種材料的熱導率和熱擴散率。In the most general case the thermal conductivity is a tensor with six components . 【ARCTIC】 導熱 貼片粉色4片裝( ... 於 www.cheshirport.co -
#77.纳米碳铜铜基石墨烯散热贴散热片贴片手机平板笔记本 ... - 京东
纳米碳铜铜基石墨烯散热贴散热片贴片手机平板笔记本散热膜绝缘胶高导热版10*10cm图片、价格、品牌样样齐全!【京东正品行货,全国配送,心动不如行动,立即购买享受更 ... 於 item.jd.com -
#78.heat sink 中文heat - Gxear
出處/學術領域英文詞彙中文詞彙; 學術名詞海事heat sink 熱匯;散熱器; 學術名詞食品科技heat sink 散熱片,發音,散熱裝置, 叫做散熱模組. “heat sink”中文翻譯吸熱 ... 於 www.forumguinurope.co -
#79.厚度0.5mm 導熱貼片高導熱導熱硅膠散熱貼絕緣 ... - HKTVmall
X37970, 屯團百貨, 厚度0.5mm 導熱貼片高導熱導熱硅膠散熱貼絕緣導熱片散熱片散熱貼片, 尺碼: A, 顏色:藍色厚度:0.5mm(約) 尺寸:100 x 100mm(約), ... 於 www.hktvmall.com -
#80.請問NVMe PCIe SSD要安裝散熱片是不是一定要撕保固貼紙啊?
我的主機板是ASUS的ROG Strix H470-I Gaming主機板上的M.2插槽有附散熱片散熱片上面有導熱貼最近買了一條金士頓的A2000 NVMe PCIe SSD安裝時發現導熱 ... 於 www.mobile01.com -
#81.散熱膏英文
10款超夯的cpu中央處理器cpu週邊散熱膏-貼片商品推薦給你. 我找的的商品都是屬於比較熱賣的商品,可以參考看看! 可能商品太多不知道怎麼選擇? 於 etwlp.got-game.org -
#82.散熱墊片
使用絕緣墊圈及絕緣導熱墊片裝在散熱片上APFC 電容採用Nichicon LGM系列470µF 450V 105 電解電容散熱墊片Spacer 兼具高導熱性(低熱阻)與柔軟性,傑勤實業有限公司 ... 於 www.guillaulles.co -
#83.25~120℃) 透明薄膜電熱片 - Heatact(ED
透明薄膜電熱片規格特性電壓:AC/DC 1-1000V 瓦特數:0.1W以上最高溫度:800 ℃ 特性•能見透明度高報85%,比傳統玻璃透明度高。 •不怕強光,貼附於螢幕畫質依然清晰。 於 www.heatact.com.tw -
#84.散熱片英文散熱片英文,thermal - Vscizr
散熱片英文 ,thermal fin中文,電子計算機名詞散熱片英文怎麼說,散熱片中文是 ... 片散熱片上面有導熱貼最近買了一條金士頓的A2000 NVMe PCIe SSD安裝時發現導熱貼的 ... 於 www.thebowrin.co -
#85.翻译'heat sink' – 字典中文-英文
散热 器. The oxide, beryllia (BeO), is used in some electronic equipment as a heat sink. 氧化铍(BeO)可用于某些电子设备,作为散热器使用。 · 散热片. en hardware ... 於 zh.glosbe.com -
#86.散热片- 维基百科,自由的百科全书
散熱 片在電子工程設計的領域中被歸類為「被動性散熱元件」,以導熱性佳、質輕、易加工之金屬(多為鋁或銅,銀則過於昂貴,一般不用)貼附於發熱表面,以複合的熱交換 ... 於 zh.wikipedia.org -
#87.散熱英文比價查詢結果
散熱英文 的比價結果,Total6筆,價格$120 To $579,1頁,Total 1頁。Biza 比價網找到更多[散熱底座],[散熱模組],[散熱鰭片],[散熱英文],[散熱鋁條],[電腦散熱], 相關產品. 於 www.biza.com.tw -
#88.cooling fin - 散熱片 - 國家教育研究院雙語詞彙
cooling fin. 以cooling fin 進行詞彙精確檢索結果. 出處/學術領域, 英文詞彙 ... 於 terms.naer.edu.tw -
#89.華宏新技股份有限公司
高導熱散熱片系列. 導熱散熱複合多功冲壓成型金屬材料. 熱導材料 · Guide Ring. Retainer Ring. 硬脆材料. 精密元件 · 新產品開發. 新產品開發. 於 www.wahhong.com -
#90.【阿哲】由熟悉的創作者設計出來的迷你機殼?! - Facebook
答案是全白鋁合金散熱片搭配石墨散熱貼. 週三 舉報. 黃仲平, profile picture. 黃仲平. 阿哲面臨財務危機被迫兼差打工辛酸畫面流出. 週三 舉報. 於 zh-hk.facebook.com -
#91.散熱片英文- 英語翻譯 - 查查在線詞典
散熱片英文 翻譯: aero fin…,點擊查查綫上辭典詳細解釋散熱片英文發音,英文單字,怎麽用英語翻譯散熱片,散熱片的英語例句用法和解釋。 於 tw.ichacha.net -
#92.導熱材料英文 - Mariposa
“儲熱材料” 英文翻譯: material for storing heat; thermal storage material. ... 導熱雙面膠READ MORE 高效能相變導熱片_ PSX EN/English CN/ 簡體中文TW/繁體中文. 於 www.mariposadesigns.me -
#93.Corsair 海盜船K70 RGB MK2 機械式鍵盤Cherry-銀軸英文版-momo ...
Corsair 海盜船K70 RGB MK2 機械式鍵盤Cherry-銀軸英文版, 內建記憶體可設定巨集1680萬色RGB可自訂背光, 紐頓e世界店家推薦!, 電腦、平板、周邊, 周邊/網路, ... 於 www.momomall.com.tw -
#94.散熱/ 導熱膏 - PChome 24h購物
Cooler Master 酷碼M.2 NVMe SSD散熱傳導貼片2入組. ☆高密度三層導熱加速元件散熱 ☆超薄設計,厚度僅0.5mm ☆自黏背貼可輕易附著SSD表層,方便使用 於 24h.pchome.com.tw -
#95.散熱片- English translation - Linguee
其SIP3封裝包含功率晶片散熱器, 當中的單列直插式全傳送模板結構,既可將印刷電路板空間減至最少,又能簡化散熱隔離及貼裝模式。 ipress.com.hk. ipress.com.hk. Its ... 於 www.linguee.com -
#96.(量大可優)1.2CM寬美國進口3M貼散熱片專用導熱膠雙面貼 ...
量大可優)1.2CM寬美國進口3M貼散熱片專用導熱膠雙面貼10CM YJ ... 3個裝12首兒童音樂芯片十二首英文音樂芯片IC 觸發更換單音芯片(D3A5) YJ. $21. 已售出215. 於 shopee.tw -
#97.导热界面材料 - 霍尼韦尔
导热界面材料(TIM)是广泛用于制造散热系统中的重要部件,以冷却和保护集成电路芯片。 ... 性,可以紧密地贴合在设备上,在降低热阻抗的同时还能减少散热片的生产成本。 於 www.honeywell.com.cn